SKF Range
Electric Gear Pumps KFU / KFUS
These pump units are designed to supply normal as well as especially large systems. Various versions are available:
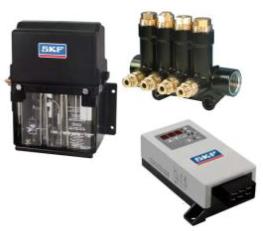
Pneumatic Piston Pump PEF-90
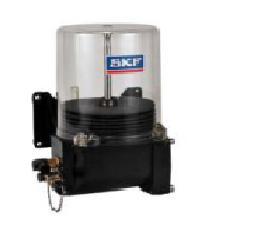
Electric Compact Unit KFB / KFBS
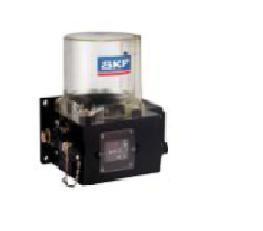
Electrically Driven Piston Pump KFG / KFGS
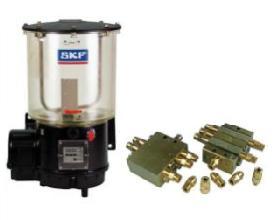
KFA / KFAS Mini-Pump Units
The pumps come in different versions:

SKF Range
Quicklube 203
Quicklube Systems have been designed to meet the severe requirements of on-road vehicles, agricultural, construction machinery and mining equipment lubrication. Their operation is based on the reliable progressive principle in which the grease is dispensed by a piston pump via progressive plunger metering devices to the lubrication point.
The lubrication occurs in metered, timed intervals at a maximum pressure of 350 bar. Thus the lubrication of bearings with high back-pressures is also guaranteed. The pump can serve up to three independent lubrication circuits consisting of numerous lubrication points with grease up to NLGI 2.
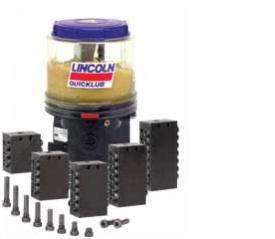
QLS 421
Accurate lubrication without the need for continuous power – that’s what over-the-road trailers need. That’s exactly what Lincoln’s QLS 421 supplies. With a unique controller card that keeps track of the time a trailer is in use by monitoring its vibration, the QLS 421 delivers the precise lubrication an OTR trailer requires exactly when it’s needed by using the power of the trailer’s brake lights.
Because it doesn’t need power to monitor the time between lubrication events, the QLS 421 is ready when its controller card says “go”. And the QLS 421 keeps lubricating each time the trailer’s brakes are applied until its controller card adds up the “on times”and determines that the pre-set time for a complete lubrication cycle has been reached.
The QLS 421 features an enhanced stirring paddle to help prevent grease separation in applications with long refill intervals.
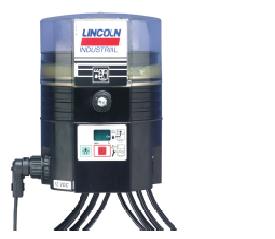
P653 Electric Centro-matic Pump
The Fully integrated P653 pump is an example of Lincoln’s commitment to providing innovative, cost effective solutions through industry-leading advances in technology. This next-generation, low-cost pump package can be fitted with one of four reservoir sizes and easily adapts to many applications.
Features:
- Integrated pump supplies lubricant to a single line parallel lubrication system.
- Pumps low and high viscosity greases including industry standard NLGI grade 2 grease.
- Easily interfaces with telematics technology in today’s heavy equipment, which enables remote monitoring of the system, indicating low level and system faults.
- Neutral switch allows mobile equipment to remain idling with pump power on but timer is deactivated – allowing manual lubrication capability at the push of a button.
Benefits:
- Integration of major system components reduces labour and overall costs.
- Simplifies lubrication system design.
- Installation time is reduced due to the ‘plug and play’ pump design. Simply mount the pump, connect the power, install the supply line and injectors and the system is ready for operation.
- Eliminates wasted grease by running only when the machine is operating.
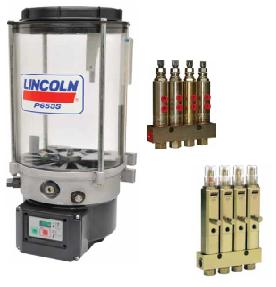
Hydraulic Bulk Fill with High/Low Level Alarm
The 03-000555BU pump is a heavy duty, hydraulically driven bulk fill pump station with the capacity to monitor high and low grease levels within the reservoir. This pump station is designed for Centromatic lubrication systems. The pump reservoir has a useable grease capacity of 20kg and 40kg, and uses a JSG High Chief pump, Lincoln electric Vent Valve, Lincoln Sonic Level device and High Level Alarm Light for remote filling of the reservoir. Because it is used mainly in harsh environments a heavy duty plastic cover is fitted to the pump station.
Features & Benefits
- BU pumps are fitted with Lincoln Sonic Sensor Level Alarms
- BU pumps can be used in conjunction with the JSG Autofill System to ensure reservoirs are not overfilled
- JSG Bulk Fill Pump Stations are NOT pressure vessels
- Available with Air, Hydraulic or Electric Pumps
- Standard grease reservoir capacity 40kg, 20kg & 15kg in the compact version
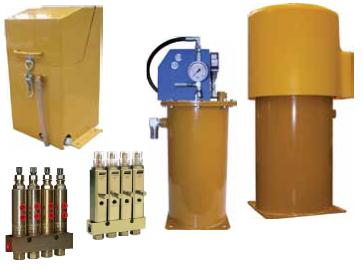
Underground Ned Kelly Pump
To meet the harsh environment of underground hard rock mining JSG developed the Ned Kelly Pump Model No. 03-002364. The design of this compact pump allows for easy installation on underground mining equipment. While the heavy duty design of the reservoir and cover aids in resisting any damage to the pump and pump components that can occur in this harsh environment.
The Model 03-002364 is an extra heavy-duty compact hydraulic pump station designed to operate a centralised lubrication system, which utilises single line parallel grease metering components. The pump is double acting, dispensing lubricant on both the Up and down strokes.
This unit is designed to be used with SL-1, SL-11, SL-32 and SL-33 series injectors or a combination of these.
The pump station incorporates all the hydraulic and electrical control components required to cycle a single line parallel grease metering system.
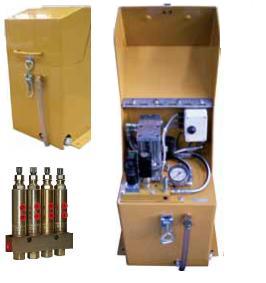